Most modern food manufacturing facilities utilize state-of-the-art conveyors, baggers, and elaborate packaging systems designed for speed, consistency, and repeatable quality. Some are OEMs, others are contract manufacturers, but all possess a shared ambition to make, pack and deliver quality manufactured foods with long shelf lives. The most data-driven companies employ sophisticated leak detection methodologies to determine package integrity. However, way too many “modern” facilities continue to use antiquated and inadequate methods, such as the water bath, to seek out packaging issues.
What is the water bath leak detection method?
According to ASTM F2096: Standard Test Method for Detecting Gross Leaks in Packaging by Internal Pressurization (Bubble Test). This test method is used as a method to evaluate package integrity. Package integrity is critical to consumer safety because heat sealed packages are intended to provide a contamination-free or sterile environment, or both, to the product. Water basin detection limits are established in the above standard.
Why is the water bath an antiquated and inadequate approach to finding leaks in food packaging?
After checking the norm and running practical tests, it turns out that in a flexible package there is an 11% chance of seeing bubbles when leaks are not present. The standard establishes a probability of 30% to detect a 75 μm leak (the diameter of a medium hair = 40 to 100 microns) Furthermore, the micro-leaks in a basin of water are not measurable because the bubbles escape through the free opening, offering the least surface tension and the slightest water column pressure.
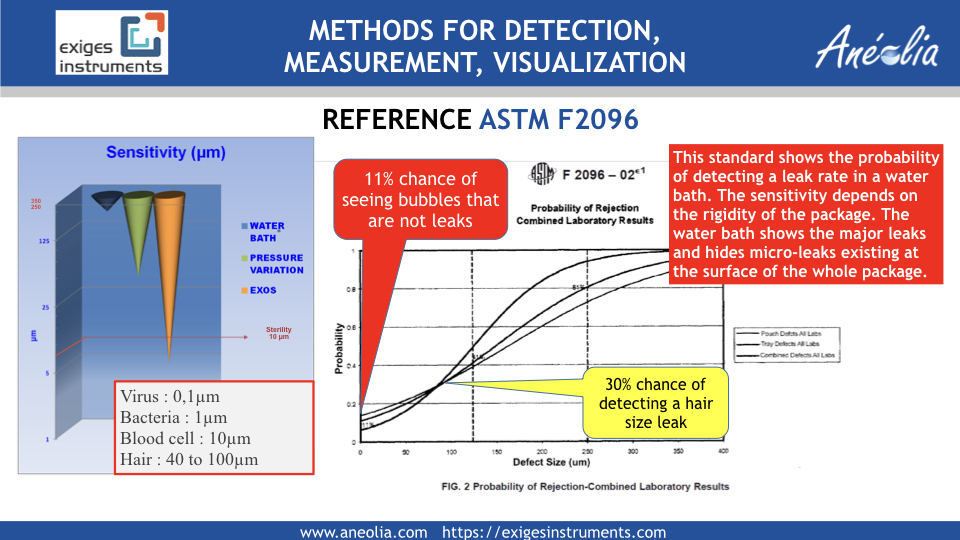
The inadequacies of water bath leak detection for food packaging:
- The absence of visible bubbles does not mean that the package is leak free. Effectively, if there are 20 holes of 5 microns each, totaling the equivalent of a 100-micron hole, these leaks are undetectable with the water bath method.
- Potential for severe hygiene problems from bacterial development within the water.
- A leak threshold value is impossible to enforce and document.
- Counting bubbles cannot provide proper traceability.
- Different operators see separate phenomenon leading to a lack of repeatability.
- The water bath is (generally) considered a “Non-destructive” method. However, the strong likelihood of water entering the package makes it unthinkable and irresponsible to insert the package back into production. Combined with the high risk of package deformation while under vacuum, we consider the water bath to be destructive.
- The gross leak can eventually be “pinpointed,” but it is irrelevant to understanding the cause and cure to the problem.
Are there better methods to ensure package integrity?
Yes, The Oxylos and Exos, designed by Aneolia are simple to operate and can detect leaks as small as 5 microns by measuring the flow rate through the package. These devices easily connect to your quality software to provide data acquisition to spot trends quickly and identify where the problem exists on the packaging line.
Recent Comments